 |
Home | Articles | Winterthur Primer: Taste or Technology? Changing Silver Borders |
|
Changing Silver Borders
|
by Ann Wagner
|
From the time America declared independence, silversmiths experimented with methods for achieving uniform and stylish ornament for their silver. During the late 1700s and early 1800s, fine hand skills required to execute engraved, flat chased, or repoussé ornament were augmented with mechanically aided methods to reduce time and effort and regularize the appearance of a design. In 1801, silversmith Thomas Bruff (1760–1816) of Chestertown, Maryland, touted such benefits when he advertised his new device for creating three silver spoons simultaneously: "This machine must certainly be an object to silversmiths, as it not only saves labour, but subjects the workman to so little loss of metal." He claimed his machine would produce as many spoons as forty hands might in an hour.1
|
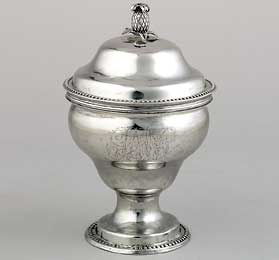 |
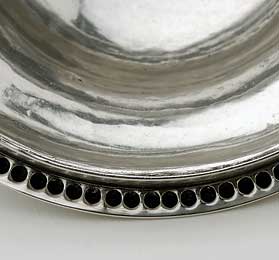 |
LEFT: Fig. 1: Sugar bowl, made by Joseph Richardson Jr. and Nathaniel Richardson (w. 1777–1790), Philadelphia, ca. 1777–1790. Silver. H. 6-3/4 in. (1990.2.2). RIGHT: Fig. 2: Detail of figure 1, underside of lid.
|
|
For example, at least three methods were used to enhance a smooth-sided vessel with beaded borders. To raise repeated circular beads, then called "pearl work," to the lid and base of a sugar bowl, silversmithing brothers Joseph Jr. and Nathaniel Richardson of Philadelphia used a round tipped punch and a hammer (Figs. 1, 2). This hand-powered technique is recognized by the slightly irregular spacing and variations in the depth of each bead.
|
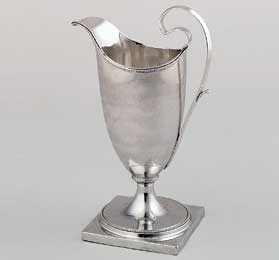 |
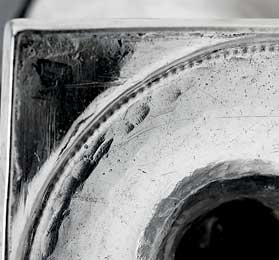 |
LEFT: Fig. 3: Cream pitcher, made by Bancroft Woodcock (w. 1754–1794), Wilmington, dated 1793. Silver. H. 6-1/8 in. (1977.168). RIGHT: Fig. 4: Detail of figure 3, underside of base.
|
|
Bancroft Woodcock of Wilmington, Delaware, employed a different method to create the beaded border for the base of a cream pitcher (Fig. 3). He likely powered a small wheel tool or mill with an iron die (pattern) to impress the beaded design directly onto the base. The underside of the base reveals the faint impression of the dies rather than hand tools (Fig. 4). The result is a border of evenly spaced beads of equal depth that are integral to the vessel.
|
 |
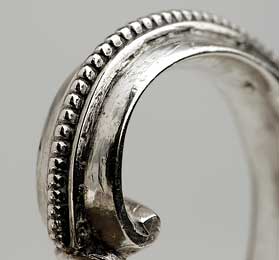 |
LEFT: Fig. 5: Cream pitcher, made by John Letelier, Sr. or Jr., (w. 1770–1810), Philadelphia or Wilmington, ca. 1770–1800. Silver. H. 6-1/2 in. (1983.86). RIGHT: Fig. 6: Detail of figure 5, handle.
|
|
A third method for making similar beaded ornament required additional silver. A thin strip of flattened silver wire impressed with a knurling tool or cranked through a hand-powered mill and impressed by a die could produce lengths of beading. Borders were then cut, conformed to the shape, and soldered onto the surface of a vessel, often to mask a soldered joint. A father and son, John Letelier, Sr. and Jr., used this type of ornament to reinforce the upper edge, shoulder, and top of the pedestal foot on their cream pitcher (Fig. 5). A small beaded strip also enhances the uppermost scroll of the handle (Fig. 6). This technique could yield yards of easily fashioned and uniformly shaped ornament for a multitude of applications.
|
 |
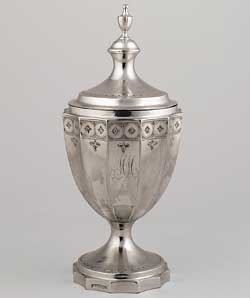 |
 |
Fig. 7: Sugar bowl, made by
Christian Wiltberger (w. 1793–1819),
Philadelphia, ca. 1793–1810.
Silver. H. 10-5/16 in. (1956.98.2).
|
By the early 1800s, prevailing tastes favored wider and more complex silver border designs. Hand skills using numerous engraving and chasing tools achieved the new look, as illustrated by the border on a sugar bowl marked by Christian Wiltberger (Fig. 7). New patterns were also cut for die-rollers to yield similar intricate borders, such as those integrated into the body of the cream pitcher made by William B. Heyer (Figs. 8, 9). Die-rolled borders could be soldered on their upper and lower edges and directly incorporated into a vessel, like the scrolling leaf borders on Heyer's cream pitcher body and base. Alternately, they could be applied to a surface, as in the repeated anthemion border that reinforces the spout (Fig. 9). Although these borders might look hand chased to the untrained eye, a few clues indicate otherwise. Their linear regularity, low-relief, and the absence of any signs of tool marks on the inside (if the border is part of the vessel wall) are telltales of the labor-saving die-rolling technique.
A wellspring of diverse border patterns, some in quite high relief, appear in American silver of the early 1800s. While research into their production and exchange between silversmiths is a topic awaiting an avid scholar, the casual observer can examine silver for indications of whether or not the maker incorporated mechanically aided methods into its design.
|
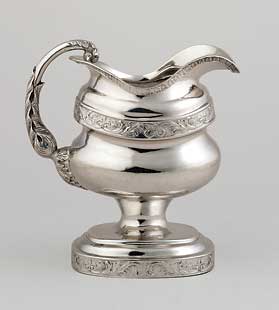 |
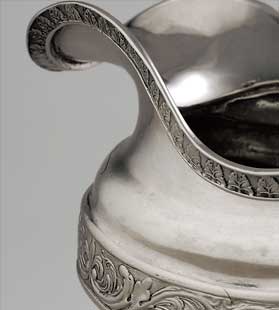 |
LEFT: Fig. 8: Cream pitcher, made by William B. Heyer (w. 1807–1828), New York, ca. 1815–1824. Silver. H. 6-1/8 in. (1966.71.4). RIGHT: Fig. 9: Detail of figure 8, spout.
|
|
|
    |
Ann Wagner is associate curator of decorative arts, Winterthur Museum & Country Estate.
She is grateful to Martha Hopkins of Hopkins Silversmiths, Baltimore, for her consultation.
All images courtesy of Winterthur Museum; photography by Laszlo Bodo.
|
|
    |
1. Advertisement "News to Silversmiths," in New-Jersey Journal (September 29, 1801): 3.
|
Download the Complete Article in PDF Format   Get Adobe Acrobat Reader
|

|
 |
 |
|
|
Antiques and Fine Art is the leading site for antique collectors, designers, and enthusiasts of art and antiques. Featuring outstanding inventory for sale from top antiques & art dealers, educational articles on fine and decorative arts, and a calendar listing upcoming antiques shows and fairs.
|